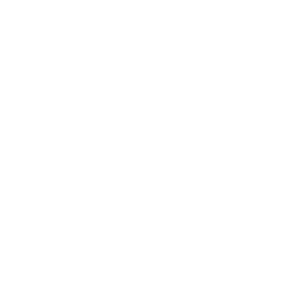
Our manufacturing facility, located in Bellville South near Cape Town, was established in 1954 and has been developed and expanded over the years to become one of the top facilities of its kind in South Africa.
Bellville Fabrication Facility
We have been serving the industry for more than 60 years, staying abreast of technological development and playing an innovative role in the engineering field. This dedication won the company the South African Institute of Welding’s Gold Medal Award in 1993 for 40 Years’ Service to industry. We have established an international reputation with exports to sub-Saharan Africa, Europe, North America, South America, the Middle East, Asia and Australia. The most recent expansion in 2014 was the addition of a 2 000 m2 factory for the manufacture of watertube boiler panels.
Bellville Factory capabilities
Cranes
Lifting capacity up to 100 ton
CNC plasma and oxy-acetylene profile cutting and flame bevelling
Largest plate size 4 m x 14 m
Guillotine
Up to 3 m wide by 12 mm thick
Plate rolling
Up to 3,2 m wide and 70 mm cold
Press brake
Up to 400 ton, knife length 3 730 mm
Hydraulic press
Up to 500 ton
Submerged arc welding machines
Max. boom travel vertically 6 100 mm / Max. boom travel horizontally 6100 mm
Thermal stress relieving
Size 21000 x 5 150 x 5 855 mm; Capacity 100 ton
Radial and traveling bed drilling machines
Max. distance outside column to spindle center 2 515 mm | Max. height under spindle 2 200 mm | Max. drill size 100mm, travel 11000 mm
CNC pipe bending
Up to 115 mm diameter – cold bending ; Above 115 mm – hot bending
Automatic panel welding
Membrane wall welding machines
Panel bending machine
Automatic economiser tube fin welding machines
Bellville Foundry
A foundry worthy of the sought-after Meehanite endorsement
Engineers who specify Meehanite® materials for the manufacturing of boilers and associated plant, have a rock-solid advantage. The patented Meehanite process ensures uniform soundness, consistent properties and dependable performance.
This is the material and design integrity that customers have come to expect from John Thompson.
The John Thompson Foundry in Bellville is worthy of the sought-after Meehanite endorsement and certified by audit to meet the required process standards for producing the family of Meehanite® irons.
Meehanite Process
All cast iron at the John Thompson foundry is produced under the Meehanite process
Boiler Castings
It is South Africa’s only foundry dedicated to boiler castings
40 Grades of Cast Iron
The Meehanite process covers the production of more than 40 grades of cast iron
Leading Foundry
The Meehanite licence is restricted to 200 of the world’s leading foundries
Guaranteed High-grade Quality
The Meehanite process involves detailed specifications, records and controls at each step of production to ensure the consistent guaranteed high-grade quality of castings demanded by the international licensor.
Isando Fabrication Facility
To provide faster manufacture, refurbishment and repair of boilers and associated plant, the John Thompson Fabrication Facility was established in 2011 in Isando, Johannesburg. It focuses in particular on the fabrication of boiler tube protection shields.
The Isando facility now offers a wider range of steel fabrication and refurbishment works, beyond boiler related projects.
Manufacturing Equipment
- Guillotine – for plate up to 16 mm thick x 3 m wide.
- Press brake – 250 ton, for plate up to 16 mm thick, with a knife length of 3,2 m.
- Plate roller – for plate thicknesses up to 20 mm x 2,4 m wide.
- Section roller for angle iron, flat bars, etc.
- Plasma cutter for stainless steel up to 32 mm thick.
Boiler tube protection shields can be manufactured for tube outside diameters of between 38 and 76 mm in carbon steel and grades 304, 310 and 316 stainless steel.
Non-Destructive Testing
To ensure that work-done meets the required quality standards, we provide a comprehensive non-destructive testing service in the following disciplines:
- Radiographic Testing (RT)
- Ultrasonic Testing (UT) including Phase Array
- Magnetic Particle Inspection (MPI)
- Dye Penetrant Inspection (DOP)
- Hardness Testing (Vickers, Brinell)
- Positive Material Identification (PMI)
- Wall Thickness Testing
- Endoscope (Internal Inspection)
All our NDT procedures and specifications are in accordance with international standards and best practices.
Boiler, boiler-related and earth moving equipment manufacturing
We manufacture:
- Boiler tube protection shields of carbon steel and 304 and 310 stainless steel with outside dimensions of between 38 and 76 mm and up to 3 m in length
- Burner spares
- Coal trollies, coal hoppers, shutter doors and ignition arches, etc
- Steel smoke stacks
- Stoker frames for industrial boilers
- Super heater elements
- Hot gas ducting
- Smokeboxes for fire tube boilers
- Earth moving equipment bushes, pins and tooling, such as TLB excavator and front-end loader buckets, etc
We Refurbish PF Burners
Please enquire about our cast metal fabrication capabilities. Shapes of virtually any degree of complexity and size can be produced, to perform consistently in any service conditions.
Certification
The John Thompson Fabrication Facility (Isando) has been assessed and certified in accordance with the requirements of:
- ISO 9001
- ISO 14001
- ISO 3834
- OHSAS 18001